Our Blow-Filling-Capping (BFC) Machine can produce PET bottles while completing the filling of drinking water and other liquids and installing bottle caps. The machine can produce PET bottles with a maximum capacity of 2.5L, and the maximum production capacity can reach 48,000 bottles per hour.
سمات
- Full 3D design and dynamic simulation testing: Advanced full 3D design technology, combined with dynamic simulation testing, to ensure the accuracy and reliability of product design.Energy-eficient preform heating sytem: The innovative design of the preform heating system not only improves the heating efficiency, but also significantly reduces energy consumption.
- New design of small and medium-sized mold base blowing staion: For the needs of medium and smal-scale production, the newly designed mold base of the molding station is more compact and efficient.
- Fast image recognition and detection technology: The use of advanced image recognition technology to achieve fast and accurate bottle
- quality inspection.
- High-speed and high-precision blowing process: By optimizing the blowing process, high-speed production is achieved while ensuring high precision and consistency of products.
Machine Parameters
Bfc Combi-block Production Line | CGX6-32-10 | CGX8-36-12 | CGX10-40-15 | CGX12-45-18 | CGX14-50-18 | CGX16-60-20 | CGX18-72-24 | CGX20-72-24 | CGX24-80-30 | |
Products Parameter | Max Capacity (ml) | 250-2000/2500 | 250-2000/2500 | 250-2000/2500 | 250-2000/2500 | 250-2000/2500 | 250-2000/2500 | 250-2000/2500 | 250-2000/2500 | 250-2000/2500 |
Max Bottle Boby Height (mm) | 340 | 340 | 340 | 340 | 340 | 340 | 340 | 340 | 340 | |
Max Bottle Body Diameter (mm) | 100/115 | 100/115 | 100/115 | 100/115 | 100/115 | 100/115 | 100/115 | 100/115 | 100/115 | |
Max Bottle Preform Height (mm) | 150 | 150 | 150 | 150 | 150 | 150 | 150 | 150 | 150 | |
Max Bottle Mouth Diameter (mm) | 38 | 38 | 38 | 38 | 38 | 38 | 38 | 38 | 38 | |
Theoretical capacity | 500ml Bottle (B/H) | 14000 | 19000 | 24000 | 28800 | 31500 | 36000 | 40000 | 43000 | 48000 |
Host Machine Parameter | Installed Capacity (KW) | 170 | 190 | 210 | 230 | 250 | 270 | 290 | 315 | 320 |
Operating Power (KW) | 60 | 65 | 75 | 90 | 105 | 120 | 135 | 165 | 170 | |
Air Capacity Consumption (m³/min) | 4.8 | 6.2 | 7.8 | 8.8 | 10.2 | 10.9 | 12.1 | 13.3 | 15.6 | |
البعد | Host Machine Size (MM) | 11000*3600*3200 | 12000*3800*3200 | 12000*3800*3200 | 13000*4600*3200 | 13000*4600*3200 | 14700*5200*3200 | 14700*5200*3200 | 15000*5300*3200 | 15000*5300*3200 |
Weight (T) | 16 | 18 | 20 | 22 | 25 | 26 | 27 | 28 | 29 |
Detailed features of the machine
- The optimized AIR heat management logic adopts the bottom-mounted heating structure of the bottle mouth to effectively maintain the bottle mouth size and heat dissipation. The 6-core 6-process high-pressure control valve is adopted to optimize the dead zone of the air path. Depending on the volume of different bottle types, the maximum recovery rate of compressed air reaches 30%, which greatly reduces the consumption of compressed air.
- High-efficiency and energy-saving preform heating system: The innovatively designed bottle heating system not only improves the heating efficiency, but also significantly reduces energy consumption.
- New small and medium-sized mold frame blowing station design: Aiming at the needs of medium and small-scale production, the newly designed blowing station mold frame is more compact and efficient.
- Full-process servo tracking and large-capacity PLC high-frequency information exchange processing ensure that each mechanical action receives a high-level rapid response and obtains extremely high automation control.
- Reverse buffer clamping technology reduces the clamping impact inertia by 40%, effectively controls noise and reduces vibration. PEEK polymer silent material is used, and the sudden change of motion inertia is passivated through professional engineering software to make the preform feeding and bottle discharging mechanism smoother and minimize the impact force.
Machine details
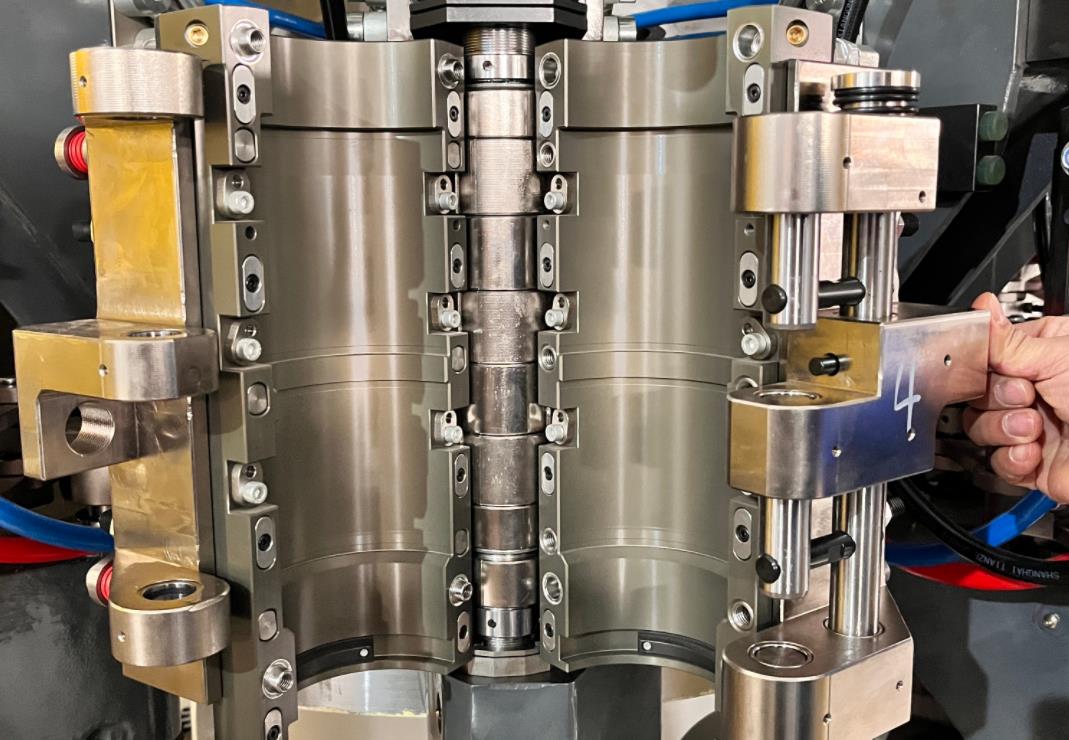
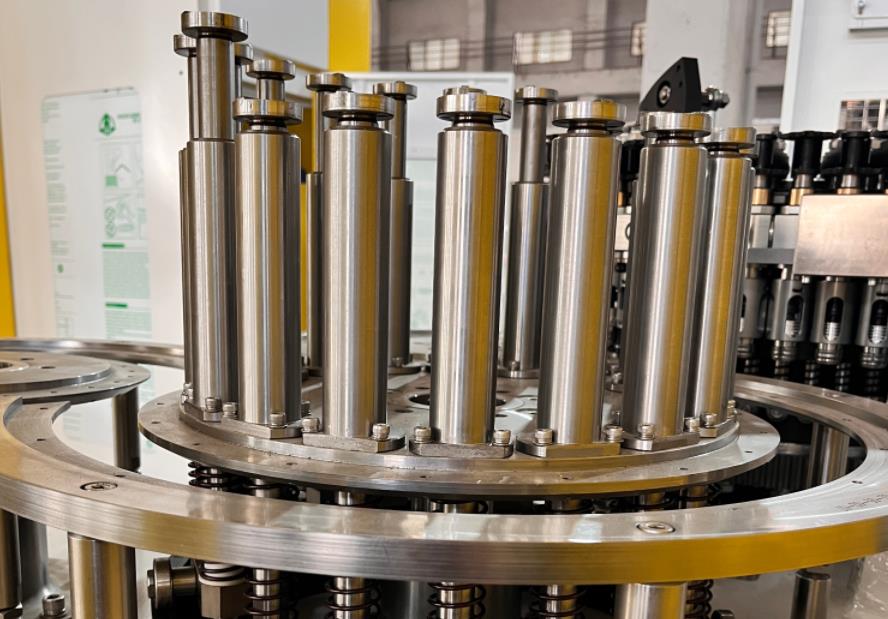
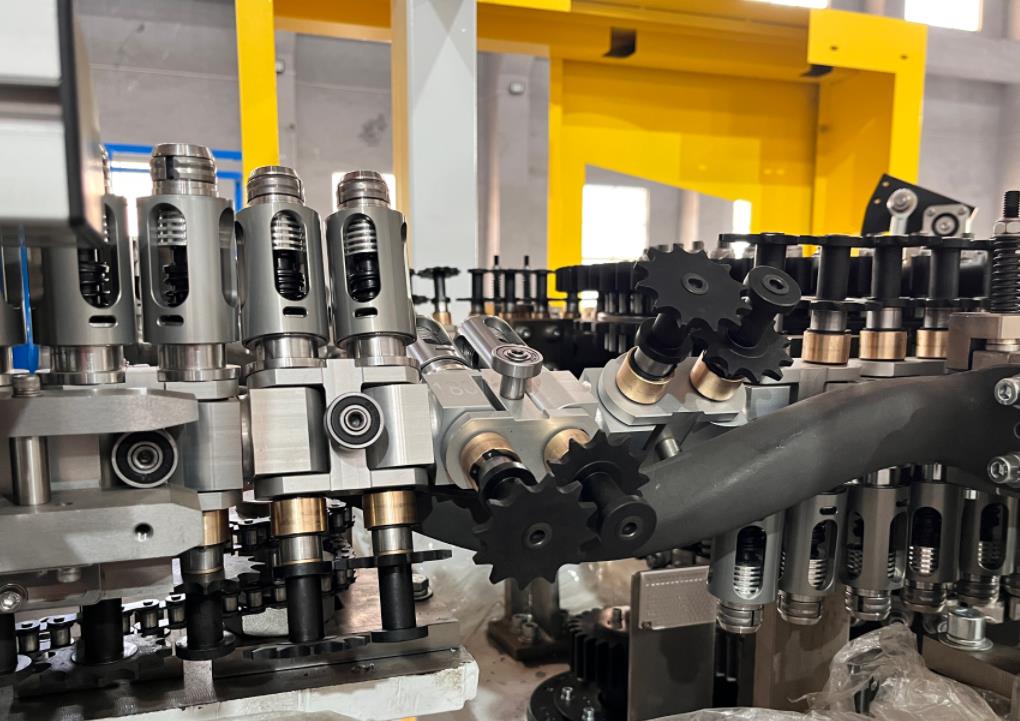
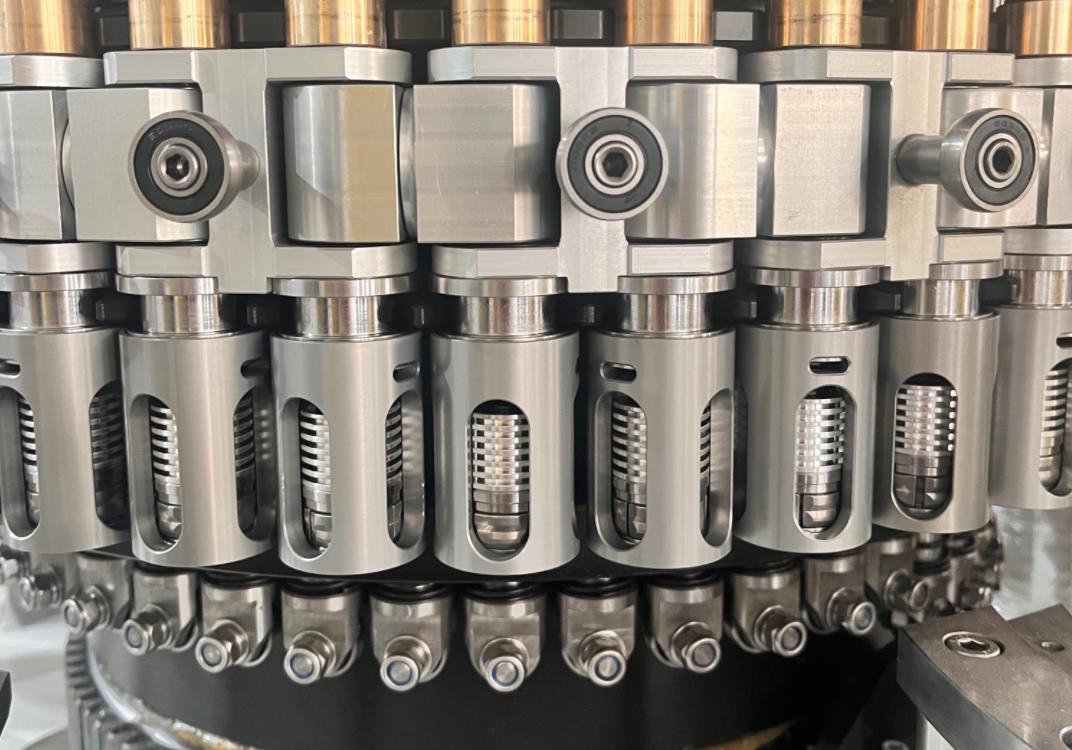
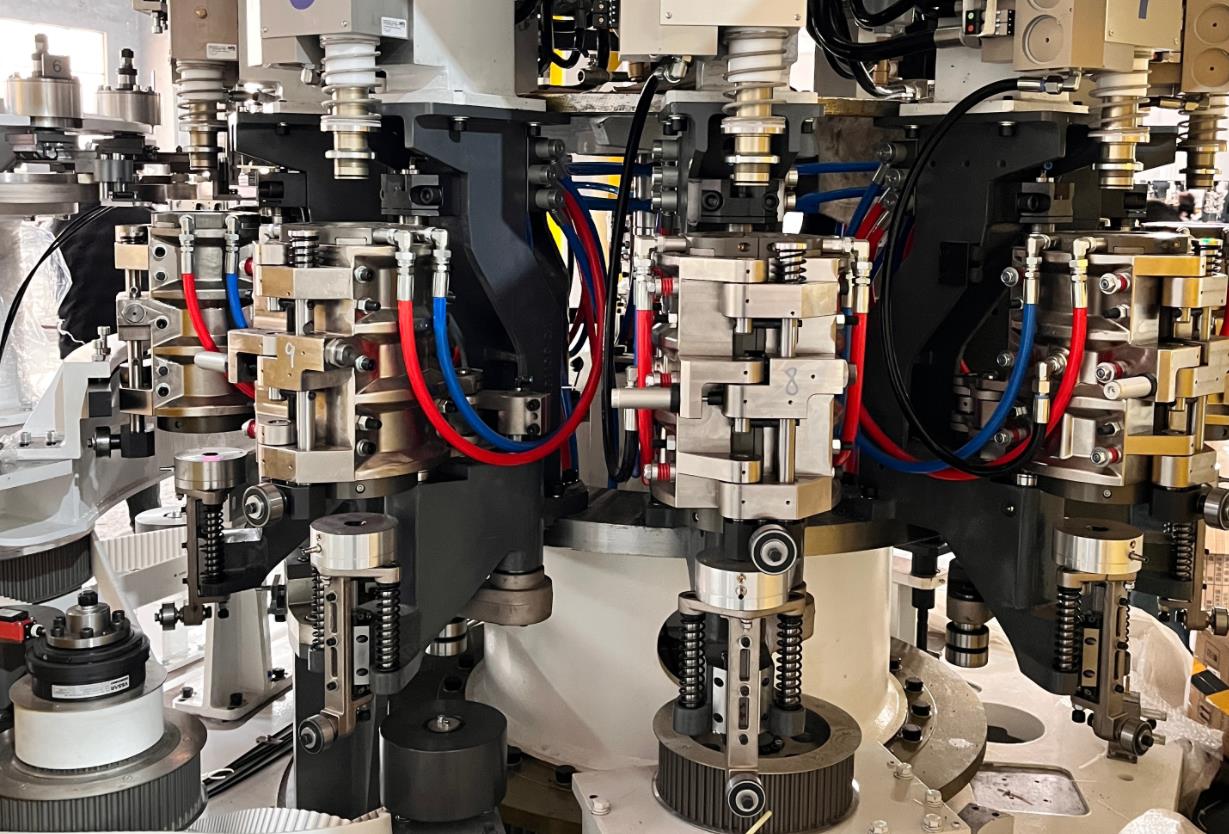
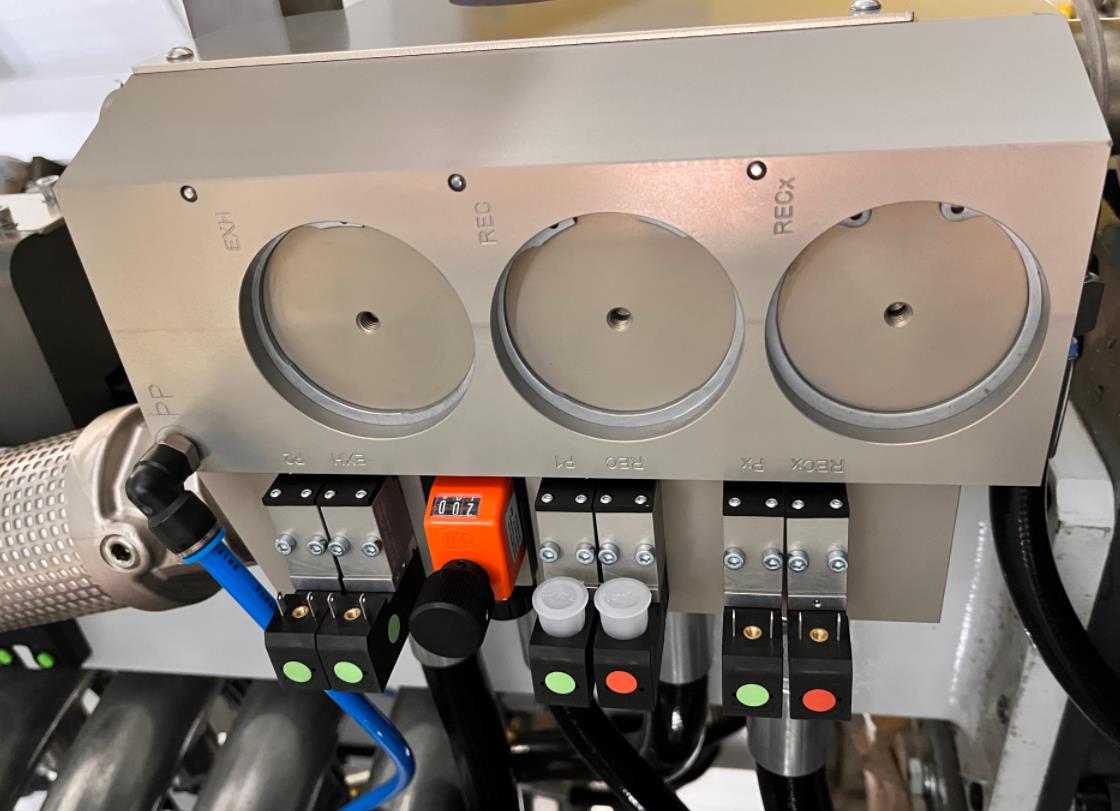